The Artisan's Touch: Advanced Scratch-Building Techniques for the Dedicated Modeler
There's a certain melancholic beauty to antique accordions. The worn bellows, the tarnished keys, the faint echo of melodies long past – they whisper tales of traveling musicians, bustling dance halls, and lives intertwined with rhythm and emotion. Holding one, you feel a tangible connection to a different era, an era where craftsmanship wasn't just about function, but about artistry, about imbuing an object with personality and soul. The same feeling resonates within the dedicated miniature railway modeler who strives to move beyond pre-manufactured components and embrace the challenge of scratch-building – of recreating a vision from raw materials, to imbue their layouts with a level of realism and originality unattainable through kits alone.
Most beginner model railroading focuses on assembly – following instructions, gluing parts, and painting. But the true passion, the deeper connection, comes from creation. It's a step up from simply assembling; it’s about understanding the fundamentals of engineering, materials science, and design, then applying that knowledge to translate a historical image or a long-cherished memory into a miniature reality. This isn't just about replicating something; it’s about interpretation, about injecting your own artistic sensibilities into the process.
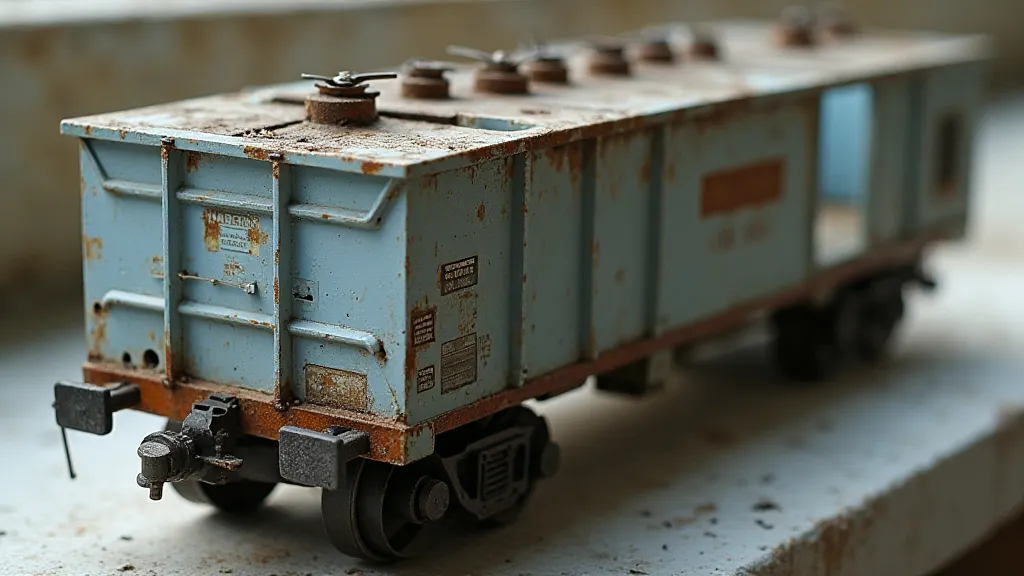
The Foundations: Materials and Tools
Venturing into advanced scratch-building requires a deeper understanding of your materials. While styrene remains a workhorse for many, experimenting with brass, wood, and even resin opens up a world of possibilities. Brass allows for incredibly fine details, simulating the look of early steel cars with a certain elegance. Wood, particularly basswood, offers a warmth and texture that styrene simply can’t match, perfect for recreating weathered wooden structures. And then there's resin – a gateway to replicating complex shapes and adding incredibly realistic details.
Tools, too, evolve beyond the basic hobby knife and glue. A good rotary tool (Dremel) is essential for shaping and cutting. Vacuum forming equipment allows you to create curved parts like roofs and car bodies. A small airbrush is crucial for achieving realistic paint finishes and weathering effects. Learning to use these tools effectively takes time and practice. Just as a seasoned accordion repairman develops a feel for the instruments, we as modelers must develop a keen sense for the properties of our materials and the nuances of our tools.
Vacuum Forming: Creating Curved Surfaces
Replicating the graceful curves of a 1930s passenger car, or the rounded profile of a weathered hopper car, is often the biggest hurdle in scratch-building. Vacuum forming is a powerful solution. The process involves heating a sheet of plastic (usually styrene) until it becomes pliable, then drawing it down over a mold using a vacuum. The mold, often crafted from plaster or epoxy putty, dictates the shape of the final part. It’s a technique requiring practice - thin walls are prone to distortion, and mold release can be tricky – but the results are transformative. It's akin to the bellows of an accordion; the air pressure and precise form are essential for creating the desired function and appearance.
Resin Casting: Reproducing Intricate Details
Sometimes, the details you need simply aren't available in styrene or brass. This is where resin casting comes into play. This involves creating a master model – a perfect representation of the part you want to replicate. This master is then used to create a mold, into which liquid resin is poured. The resin hardens, creating a copy of the master. Resin casting is fantastic for replicating small, complex parts like locomotive details, interior components, or even entire buildings. The process can be messy and requires careful handling of chemicals, but the ability to reproduce incredibly detailed parts is a significant advantage. It's the dedication of a craftsman who painstakingly restores an old accordion, carefully preserving every detail and ensuring its continued functionality.
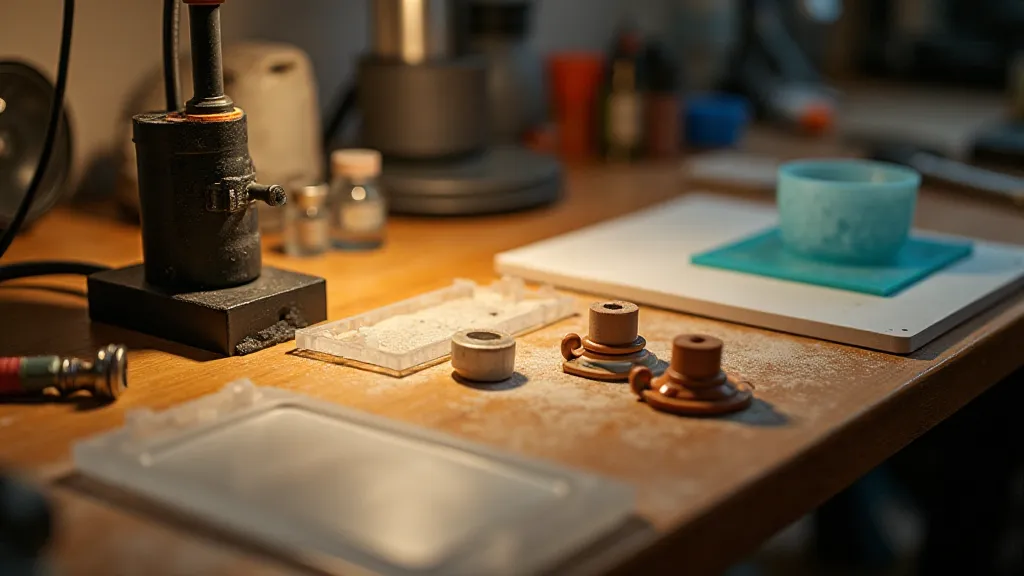
Beyond the Materials: Achieving Realism Through Weathering
Even the most meticulously crafted models can fall flat if they lack weathering and detailing. This is where artistic interpretation truly comes into play. Consider the weathered appearance of a real-world railroad car – the streaks of rust, the grime accumulation, the chipped paint. These aren’t flaws; they are testament to a history of use, of exposure to the elements, of the passage of time. Mastering miniature weathering techniques – dry brushing, washes, pigments – is crucial for creating a believable scene. The same principle applies to an antique accordion – the cracks in the finish, the faded ornamentation – these aren’t signs of decay, they are markers of a life lived, of melodies played and memories cherished.
Scratch-Built Train Cars: A Labor of Love
The pinnacle of scratch-building is, arguably, constructing entire train cars from raw materials. This is a project that demands patience, precision, and a deep understanding of railroad car construction. It’s not just about assembling parts; it’s about replicating the intricate details of the prototype – the brake rigging, the air lines, the undercarriage. It's a deep dive into a historical subject, understanding the evolution of design and the interplay of function and form. It’s a commitment akin to a restorer working on a rare and complex instrument, a commitment to preserving a piece of history. The satisfaction of watching that car, born from your own hands, move along your miniature railroad is unparalleled.
Layout Design Guide: Integrating Scratch-Built Models
Scratch-built models shouldn't exist in isolation. They should be thoughtfully integrated into your layout’s overall design. Consider the scale, the era, the geographical location. A meticulously crafted scratch-built engine won't feel authentic if it's running on a modern, high-ball layout. Think about the background – the terrain, the vegetation, the structures. Everything should work together to create a cohesive and believable scene.
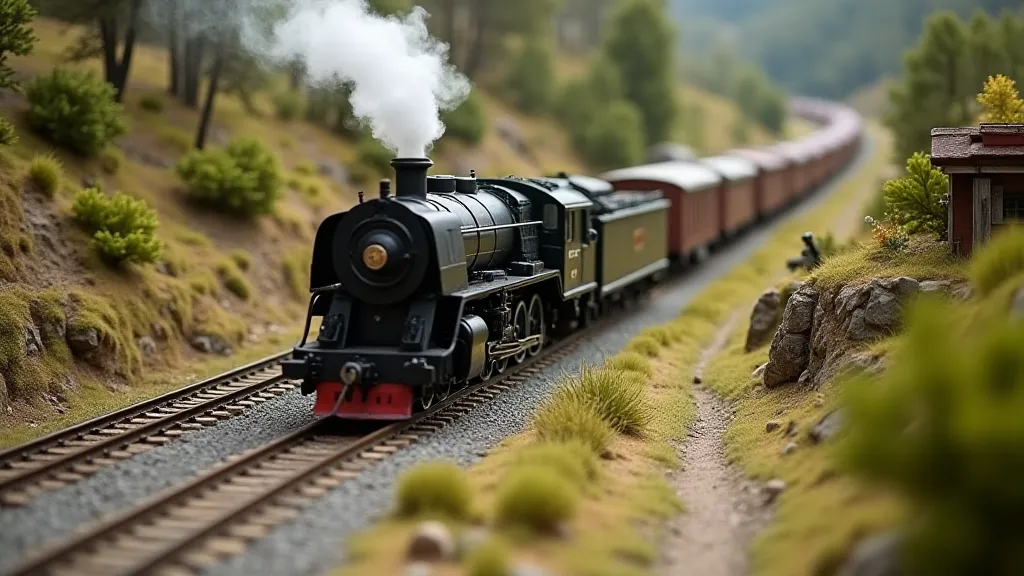
Troubleshooting & The Eternal Learning Process
Scratch-building is not without its challenges. Parts may warp, resin may bubble, paint may not adhere properly. These are inevitable setbacks, but they are also opportunities for learning. Each failure brings you closer to understanding the intricacies of the process. The key is to be observant, to experiment, and to never be afraid to try something new. Just as an accordion player refines their technique through years of practice, we as modelers must embrace the continuous process of learning and improvement.
The artisan’s touch isn’s just about skill; it’s about passion, dedication, and a deep appreciation for the craft. It's about striving for excellence, not just in the final product, but in the entire process. It's about finding joy in the creation, in the challenge, and in the enduring legacy of your miniature world.